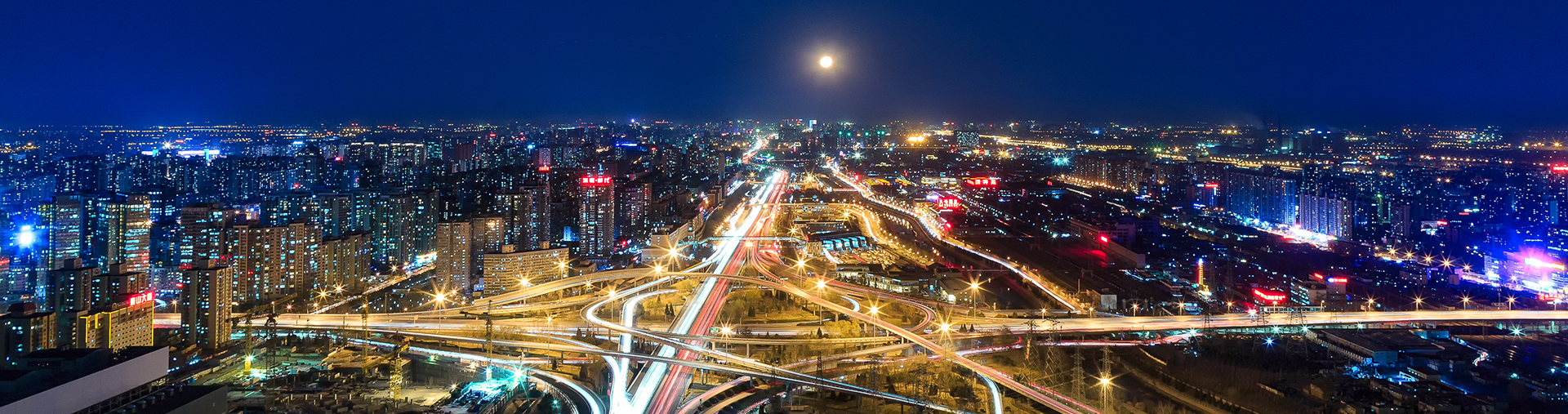
- DB-3172S Aluminium special glue manual
- DB-3172 Aluminum Foil Special Adhesive Manual
- DB-3175L low viscosity ordinary glue instructions
- DB-3175 ordinary glue manual
- DB-3250 anti-medium special glue manual
- DB-3266 medium temperature cooking instructions
- DB-3366 135 degree high temperature glue manual
- DB-6691 solvent-free two-component polyurethane adhesive instructions
- DB-6692 solvent-free two-component polyurethane adhesive instructions
DB-3250 anti-medium special glue manual
- Categories:Product Technical Manual
- Time of issue:2020-06-18 00:00:00
- Views:0
DB-3250A/B type is a two-component polyurethane adhesive, which has a good composite effect on products containing aluminum foil structure. The plastic/plastic composite product can withstand boiling below 121℃.
One. Performance characteristics
1. Plastic/plastic composite products can withstand high temperature sterilization below 121℃ for 30 minutes.
2. Used in PET//AL//CPP, PA//AL//CPP, PA//AL//PE, PET//AL//PE and other structures.
3. It has excellent resistance to content and humidity and heat.
4. This product has good resistance to acid and spicy media, and is suitable for packaging seasoning packets and Sichuan pickles.
5. The composite film has good transparency and flexibility.
Two. Physical properties
Product name | DB-3250A main agent | DB-3250B curing agent |
Exterior | Light yellow transparent liquid | Colorless or light yellow transparent liquid |
Solid content (%) |
50±2 |
75±2 |
Viscosity mPa.s (25℃) |
1000±200 |
1500±500 |
Proportion (weight) |
20 |
4 |
1. Standard ratio (weight ratio): Main agent: curing agent=20:4, when the air humidity is high (more than 70%) when printing with polyurethane ink, the curing agent must be increased by 10-20%.
2. Dilution: first calculate and weigh out the ethyl acetate required for a certain working concentration (the water content of ethyl acetate cannot exceed 200ppm, and it is not allowed to contain alcohol, amine and other compound impurities), and then transfer to the main agent of known weight Add ethyl acetate and stir fully in a fixed direction (for example, clockwise), add the curing agent after it is uniform, and stir again. It is best to mix the whole barrel of the main agent with the whole barrel of curing agent, because the curing dose is small, and the weighing accuracy will not be high if it is divided into several times. The viscosity of the solution should be considered when calculating the working concentration, because the viscosity will affect the coating amount and coating state.
3. The change of standard ratio and solvent comparison table and working fluid with the same viscosity
Working concentration (%) | Main agent (kg) | Curing agent (kg) | Thinner (kg) | Viscosity (zahn3# cup/25℃) second |
35% | 20 | 4 | 13.14 | 19.44 |
33% | 20 | 4 | 15.4 | 17.50 |
30% | 20 | 4 | 19.33 | 14.94 |
27% | 20 | 4 | 24.15 | 13.60 |
25% | 20 | 4 | 28 | 12.63 |
4. Coating amount calculation: There is a rough empirical formula for calculating the coating amount of Bumeilan and laser coating rollers for reference:
Coating amount on dry basis (g/㎡)=0.2×Working fluid concentration%×Mesh depth µ×Working fluid specific gravity
The above formula cannot be applied to the electro-engraved coating roller and the pyramid-shaped embossing coating roller. The proportion of the working solution concentration of 41% is 1; the proportion of the concentration of 26% is 0.96. The proportion of calculations with low accuracy can be ignored.
5. Selection of coating amount: The coating amount (dry basis) cannot be less than 3.5g/㎡, and the anti-medium packaging can be appropriately reduced. The coating amount requirements are constant, which is not a concept with the statistical average. The heat resistance of the adhesive firstly depends on the degree of drying. The prerequisite for increasing the coating amount is to ensure complete drying. The degree of surface treatment of the substrate film also affects the peel strength, especially PET, PA and AL.
6. Drying: In order to make the solvent in the base film coating layer evaporate cleanly, the drying efficiency of the dryer should be improved as much as possible. The factors that affect the drying efficiency are hot air temperature, wind speed and air volume. The faster the compounding speed, the higher the drying efficiency requirements; on the contrary, when the equipment drying efficiency is low, the compounding speed can only be reduced.
The wind speed and air volume of the compound machine are generally not adjusted frequently after correction, but the hot air temperature and compound speed often change. The principle of setting the hot air temperature is to low first and then high to form a temperature gradient. The purpose is to prevent the coating surface from drying too quickly and preventing the further volatilization of the internal solvent. This is often called "false drying". For example, when the nozzle wind speed of the drying box is 30 meters per second and the composite speed is about 80 meters, the hot air can be set at 50-60°C, 60-70°C, 70-80°C, depending on the substrate and coating amount.
7. Laminating: On the premise that the film is not overstretched or damaged, the temperature of the composite hot roller should be increased as much as possible, and the temperature of the hot roller can be selected between 50 and 85 ℃. Note: The temperature of the heating cylinder is not equal to the temperature of the heat roller, and the temperature of the edge of the heat roller is not equal to the temperature in the middle of the heat roller. The line pressure of the hot roller is determined by the cylinder diameter, air pressure, hardness and length of the silicone roller. The only thing that can be adjusted frequently is the air pressure. Different composite machines cannot compare the linear pressure of the heat roller with the reading of the pressure gauge.
8. Curing: The composite film from the machine should be sent to the curing chamber as soon as possible, and the composite film should be heated at 50~60℃. The uncured adhesive will melt and level, eliminate small bubbles and white spots. After continuous curing for 72 hours Able to achieve satisfactory bonding strength. The air in the maturing room is required to circulate and flow, the purpose is to make the temperature of the maturing room consistent; the air with high solvent content in the maturing room is continuously discharged, and the solvent concentration in the indoor air is reduced through convection, which is beneficial to the continued volatilization of the residual solvent in the composite film.
Four, matters needing attention:
1. The amount of glue to be dispensed is determined according to the needs. It is ready for use now. It is best to use up the glue on the same day. The remaining glue cannot be used in principle. If there is too much glue left, it can be diluted several times with a solvent and put in a closed container and stored in a cool and dry place. When working on the next day, use the remaining glue as a diluent in a small amount (about 20% or less) into the newly prepared glue. Use in liquid (degraded use). If white turbidity, translucency and viscosity increase are found, it should not be used again.
2. Composite substrates such as BOPET, BOPA, CPP and other films require surface treatment. The surface tension of cooking grade CPP requires more than 39 dyne, and BOPET and BOPA both need to be more than 52 dyne. AL must ensure that the annealing and degreasing are clean; BOPET and BOPA that are not treated on both sides cannot be laminated on both sides in principle, otherwise the peel strength of the non-corona side cannot be guaranteed.
3. The technical opinions provided in this manual are from sincerity and are for reference only. Since each user's equipment, process and raw materials are not controlled by our factory, the user is also responsible for experimenting with the products provided by our factory to verify whether it is suitable for the proposed process and purpose.
4. Due to the continuous advancement of technology, the company has the right to modify this manual. When the manual is changed, we will not notify you separately. When you use the manual, please confirm the latest version. If there is any ambiguity, please contact us in time.
5. This product is flammable, so be careful when using it.
Five, packaging and storage
Main agent 20kg/barrel, curing agent 4kg/barrel.
This product should be placed in a cool and dry place. The storage period of the main agent is 12 months, and the storage period of the curing agent is 9 months. After opening the package, it should be used up as soon as possible, and no more storage.
Scan the QR code to read on your phone
Copyright Zhejiang Duobang New Material Co., Ltd. all rights reserved

www.300.cn

Copyright Zhejiang Duobang New Material Co., Ltd. all rights reserved www.300.cn